AAC Block and Panel Production Line in Bangladesh
Zihan Tech is the only supplier of the Donyue AAC Block and Panel Production Line in Bangladesh. As the building sector expands, there is a greater demand for stronger, lighter, and more environmentally friendly materials. AAC (Autoclaved Aerated Concrete) blocks are transforming the way we construct. These are lightweight, resilient, and energy-efficient.
This Block Production Line allows you to make high-quality AAC blocks that fulfill modern construction specifications while saving time and money. AAC blocks are suitable for residential, commercial, and industrial buildings. These lines offer superior thermal insulation, fire resistance, and soundproofing. Furthermore, its lightweight design makes it easy to transport and manage.
Join the construction revolution with the DONYUE AAC Block Production Line. Call us at +8801841119091 to learn more about us!
Ask for a Free Quotation!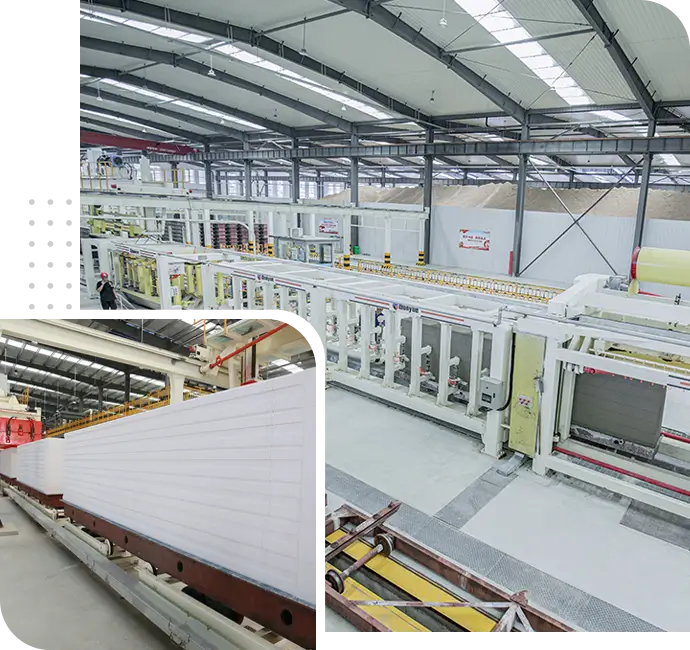
Layout of AAC Block & Panel Production Line
The layout of an AAC block and panel production line is intended to ensure smooth and efficient manufacturing. Each stage is designed to maximize efficiency, decrease waste, and ensure high product quality.
Here is the layout of the AAC block production line:
- 1. Raw material processing section
- 2. Batching, pouring & curing section
- 3. Steel cage preparation section
- 4. Cutting & grouping section
- 5. Autoclave curing section
- 6. Finished product packaging section
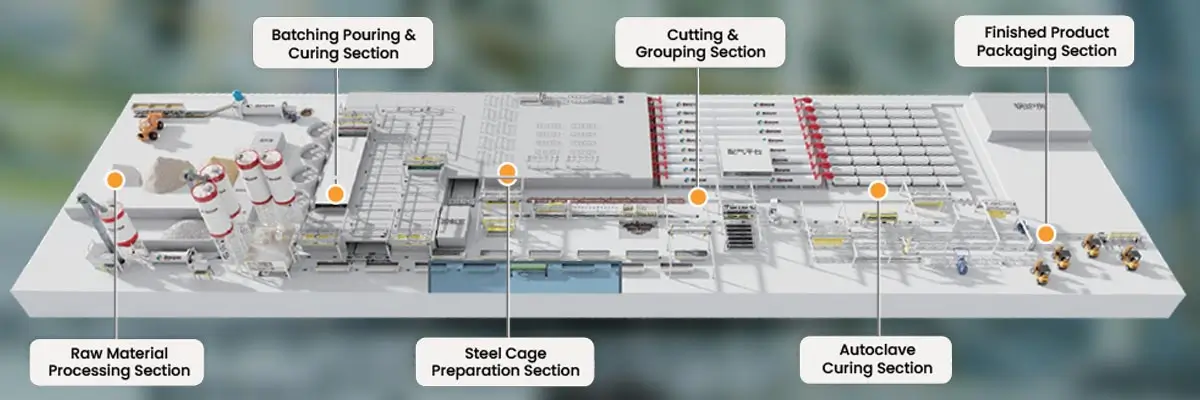
Raw material processing section
The raw material processing stage is the initial step in creating AAC blocks and panels. This division prepares key materials such as cement, lime, sand, fly ash, and aluminum powder. These materials are treated by machinery such as crushers, ball mills, and bucket elevators.
The machines grind, combine, and transport the materials to ensure that they satisfy the appropriate standards. After processing, the materials are kept in silos or containers, ready for the next steps. This part establishes the foundation for the entire production process, hence it is a vital stage in generating reliable products.
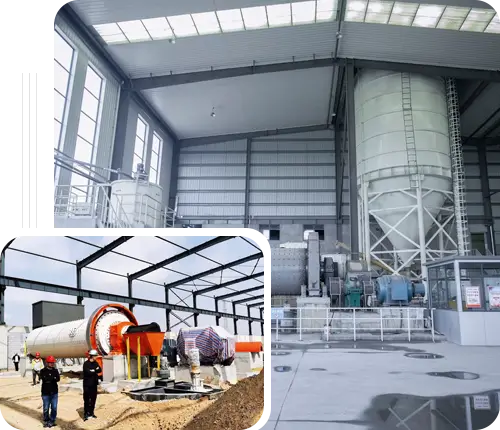
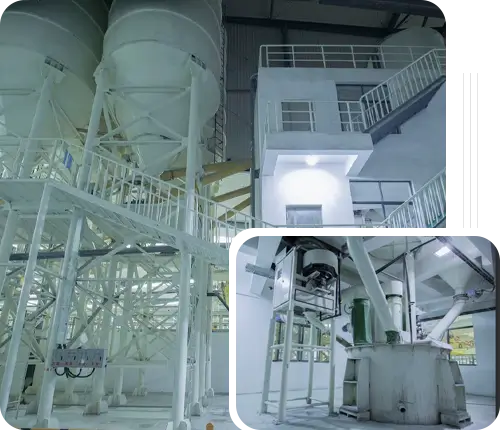
Batching, pouring & curing section
These stages are very important in the AAC block and panel manufacturing process. Raw ingredients such as cement, sand, lime, and aluminum powder are precisely combined utilizing automated batching equipment. The slurry is placed into molds and starts to react and expand.
During this stage, the steel mesh cage is carefully put into the slurry to strengthen the finished product. This step guarantees that the combination is strong enough to cut and further process. This area is built for efficiency and precision, guaranteeing that each product fulfills high-quality requirements.
Steel cage preparation section
The steel cage preparation section is vital for producing sturdy AAC panels. This section covers the creation and handling of steel cages (or meshes) used to reinforce the panels. The cages are precisely manufactured to ensure the end product's longevity and stability. Here are the main steps in this section:
- Raw material check
- Cutting
- Welding
- Shape adjustment
- Inspection
- Automation
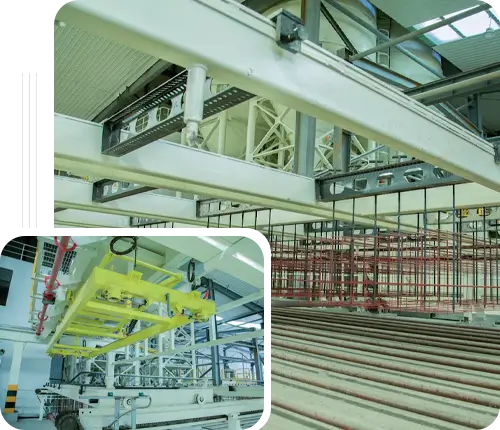
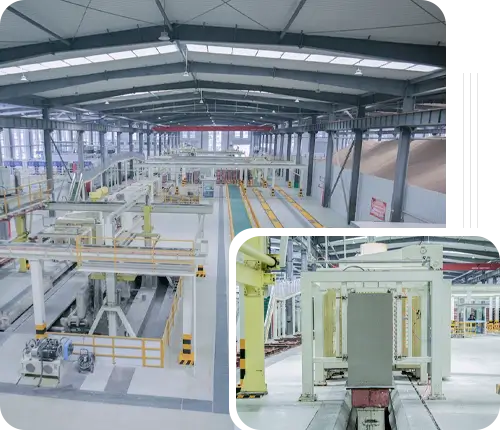
Cutting & grouping section
It is an important aspect of the AAC production process. During this stage, the green cake formed during the curing stage is ready for final molding. The green cake is carefully transferred to the cutting area by specific devices such as tilting hoists and cutting carts.
After cutting, the grouped blocks and panels are prepared for the next stage. The chopped pieces are organized in a systematic order to ensure easy handling and transit to the autoclaving area. The grouping method guarantees that the items are neatly ordered and sturdy while curing.
Autoclave curing section
The autoclave curing section is the final stage of the AAC production process. Green cakes are bundled after being cut and delivered to large autoclaves. In these sealed rooms, the goods are subjected to extreme pressure and temperature. This approach allows the chemical processes to conclude, resulting in AAC products that are lightweight, strong, and fire-resistant. Key Features of the Autoclave Curing Section:
- High pressure
- Steam usage
- Large capacity
- Efficient process
- Green technology
- Energy recovery
- Safe handling
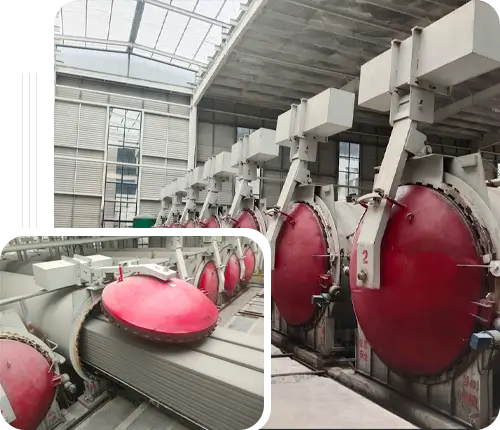
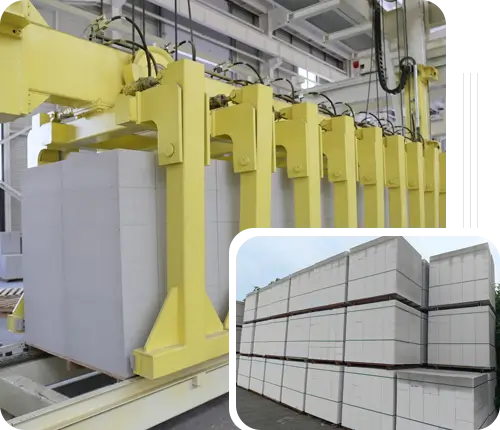
Finished product packaging section
The AAC block and panel manufacturing process concludes with the finished product packing department. After the blocks and panels have fully cured in the autoclave, these are carefully removed and brought to this section. Minor flaws or challenges are addressed before the packaging process begins.
The blocks and panels are then carefully packed to prevent breakage and ready for shipping. Following inspection and stacking, the blocks are securely wrapped in protective layers to avoid damage during shipment and handling.
Advantages of AAC Block and Panel Production Line
The AAC block production line has various advantages. This innovative manufacturing technology assures maximum efficiency and produces high-quality blocks with little waste. It helps to reduce costs while satisfying environmental criteria, making it a viable choice.
Here are some advantages:
-
Lightweight
AAC blocks are almost 60% lighter than traditional bricks. It reduces the overall weight of a building. Lightweight blocks also help lower the structural load.
-
Fire-resistant
AAC blocks are resistant to high temperatures for extended periods. These blocks provide excellent fire safety for buildings. This ensures better protection.
-
Sound insulation
These have superior soundproofing properties. AAC blocks help in minimizing outside noise. It is ideal for urban and industrial settings.
-
Energy efficiency
These blocks are very good in thermal insulation. It keeps the building cool during summer and warm during winter.
-
Eco-friendly
AAC block manufacturing requires less raw material. These blocks are prepared with recyclable materials. It reduces the carbon footprint.
-
Cost-effective
AAC blocks are cheaper than conventional bricks. It requires less mortar during construction. Affordability makes it accessible for more projects.
-
High compressive strength
These blocks are strong enough and durable. Its high strength ensures lasting construction quality. Most builders rely on AAC blocks for hassle-free performance.
-
Easy to handle
AAC blocks are lightweight and highly accurate in size. They are thus easy to cut, shape, and install. Workers can manipulate them with very little effort.
-
Fast production
The manufacturing process of AAC blocks is efficient. It reduces the time required to produce blocks.
-
Versatile
It is suitable for both wall and partition uses, even to the point of roofs. In many ways, it helps the builder in executing projects of varying natures, hence their popularity.